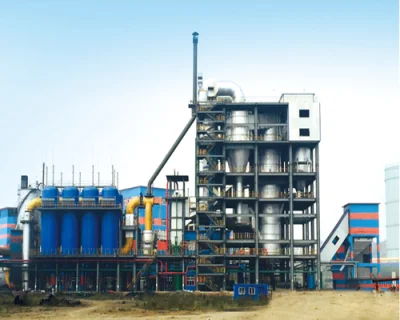
Генератор газификатора биомассы Huangtai
Современное состояние процесса газификации угля с использованием синтетического композиционного порошка. Газификация угл;
Базовая информация
Модель №. | HT-21072202-G |
Состояние | Ной |
Сертификация | ИСО |
Период доставки | Шесть месяцев |
Транспортный пакет | Контейнер |
Спецификация | 50000 Нм3/ч |
товарный знак | ХТ |
Источник | Женщины |
Описание продукта
- Современное состояние процесса газификации угля из синтетического композиционного порошка
Газификация угля является лидером современной углехимической промышленности и делится на технологии синтетической газификации и газовой газификации.
На уголь, используемый в качестве топлива, приходится более 85% производства. С улучшением требований по защите окружающей среды PM2,5 производство электроэнергии на промышленном газе, отечественном синтетическом природном газе, IGCC и высокотемпературных топливных элементах станет неизбежной тенденцией. Спрос на газификацию угля с высоким содержанием метана резко увеличился, что составит более 80% будущей газификации угля.
Существующая современная технология газификации угля на основе газа представляет собой только газификацию с подвижным слоем Lurgi, но сточные воды, образующиеся в результате гудрона, являются узким местом в ее производстве и применении.
- Процесс газификации угля из синтетического композиционного порошка
Введение процесса
Синтетическое композитное устройство для газификации пылеугольного топлива представляет собой газификатор, состоящий из циркулирующего псевдоожиженного слоя, импульсного транспортирующего слоя и увлеченного слоя. После измельчения сырого угля пылевидный уголь диаметром 6 мм отправляется из секции подготовки угля в угольный бункер газификатора. Уголь подается в нижнюю часть кипящего слоя комбинированного газификатора через шнековый конвейер в нижней части угольного бункера. В качестве агента газификации и среды псевдоожижения воздух или кислород предварительно нагреваются и смешиваются с перегретым паром низкого давления. Он поступает в печь газификации через воздухораспределительную пластину в нижней части псевдоожиженного слоя и поступает в печь при температуре 1000 °C для сгорания и реакции газификации. CO, H2, CO2 и т. д., высокотемпературные твердые частицы классифицируются и отделяются в верхнем конце газификатора с помощью горизонтального быстрого сепаратора, а крупные и средние частицы возвращаются в нижний конец карбюратора через рециркуляционное устройство для сгорания и реакция газификации. Мелкодисперсная углеродистая зола-уноса поступает в увлеченный слой в нижней части комбинированного газификатора, где подвергается высокотемпературной шлаковой газификации при температуре от 1300°С до 1500°С, а расплавленный жидкий шлак возвращается в нижнюю часть газогенератора. композитный газификатор.Газификатор осуществляет теплообмен с псевдоожиженным материалом. Он охлаждается и затвердевает, а теплота фазового перехода жидкого шлака восстанавливается, чтобы обеспечить часть тепла для реакции газификации угля. Твердый шлак окончательно выгружается из нижней части печи и после теплообмена и охлаждения отправляется в шлаковое поле. Газ направляется в бензобак после рекуперации отходящего тепла, удаления пыли и других очистительных процедур, чтобы обеспечить газом следующую секцию. Вышеуказанные мероприятия решают проблему рвоты и диареи в циркулирующем кипящем слое, устраняют летучую золу и снижают содержание метана в синтез-газе, что положительно влияет на реакцию синтеза последующей системы.
- Технологические характеристики формирования композиционного порошка газификации углей
Вам также может понравиться
Отправить запрос
Отправить сейчас